The expert's view: David Gómez, director of the Laser Manufacturing Lab at Tekniker
Laser technology offers the industry very interesting benefits. In fact, the use of lasers in the area of industrial manufacturing provides the greatest source of income for the sector with nearly 41% of the market compared with other applications. Tekniker, an expert in laser for manufacturing, offers an overview on the current status of this technology as well as information concerning future developments based on its experience in terms of assisting companies to address this challenge.
The use of lasers in the area of industrial manufacturing represents the greatest source of income for the sector with nearly 41% of the market compared to applications such as communications (27%), safety and defence (12%), sensorics (9%) and the medical sector (8%)1.
Generally speaking, industrial lasers are currently used in solidly established processes such as cutting, welding, heat treatments or marking. They also represent a key element as regards developing innovative processes such as additive manufacturing or high-speed texturising.
Unlike other types of sources, industrial lasers must feature specific characteristics such as the capacity to provide amplification at high power settings, a compact design allowing for their incorporation to industrial systems and also enable robust manufacturing to combine reliability and stability in 24/7 environments.
Fundamentally, there are nowadays four types of industrial lasers that incorporate these characteristics in a number of active media and which are, namely, CO2 lasers, solid state lasers, diode lasers and fibre lasers.
It is important to underscore a growing interest on the part of the industry with regard to fibre lasers that have a market share figures above 50% and more growth is expected to occur over the next few years.
Likewise, it must also be borne in mind that the technological complexity of an industrial laser whose emission is defined in terms of wavelength (specific for each active medium) and a given power profile (generally Gaussian), means that the market is dominated by large corporations and that the only market share available to small companies is related to more specific applications such as the development of ultrashort pulse lasers.
In this context, our fundamental aim is to summarise the current status of technologies and components which, based on the emissions produced by these industrial sources, do not only make it possible to implement efficient and resilient manufacturing systems but also provide guidelines to develop new manufacturing processes.

Modifying the characteristics of a laser beam: wavelength and shaping
Laser emission wavelengths are like the “fingerprint” of each active medium used. Generally speaking, it can be stated that, with the sole exception of CO2 lasers, conventional industrial lasers feature active mediums emitting in the infrared region close to the (900nm-1100nm) spectrum.
In certain cases, it is necessary to use shorter wavelengths to increase or enable the processing of certain materials that are clearly different in terms of their optical properties in these zones of the spectrum. A clear example can be seen in this case of copper welding as absorption in 400nm reaches 65% compared to 5% at 1000nm.
The use of these ultraviolet lasers is especially attractive mainly due to how relevant this process is with regard to developing electromobility solutions.
Similarly, these so-called “triplicate” lasers facilitate micro-manufacturing actions involving polymeric materials commonly used in the health care sector. Likewise, “green” lasers are gradually being introduced in SLM (Selective Laser Melting) additive manufacturing processes to facilitate and speed up the production of materials that have been somewhat uncommon until now.
All of the above is possible thanks to the so-called spectral conversion crystals (LBO, BBO, KTP, etc.) which, based on non-linear optical phenomena, make it possible to multiply emission frequencies and, consequently, diminish the fundamental wavelength of a laser system in integer multiples of their fundamental wavelength.
Consequently, when using a solid-state laser with emissions at 1064nm (Nd.YAG) they can be “doubled” (532nm), “tripled” (355nm) or “quadrupled” (266nm) to obtain lower wavelengths with end power losses of 50%, 67% or 75%, respectively.
An effect inherent to this spectral conversion is a reduction in the size of the laser spot which in some case provides an additional motivation to use these techniques.

As in the previous case, conventional emissions of industrial lasers occur in the so-called fundamental mode, TEM00, that produces a Gaussian distribution of emission intensity. The M2 parameter defines the quality of the Gaussian beam and allocates a M2=1 value to a perfect gaussian profile and considers that high quality beams are those with M2 ranging between 1 and 1.5.
There are, however, applications for which it is desirable to have an alternative spatial profile that an optical element must be incorporated to obtain this non-gaussian distribution. The most widespread example is related to the obtention of square profiles (Top-Hat) by using refractive optics or diffractive optical elements (DOE). These are used, for instance, in applications that require completely vertical walls in drilling and cutting operations.
Likewise, the cutting of transparent materials can benefit from converting the Gaussian beam into a Bessel beam to ensure excellent focal depth throughout the entire glass profile. These techniques are currently applied in sectors such as electronics (to cut LCD screens) or luxury goods (to bevel watch spheres).
In recent years, beam shaping inside optical fibres has become highly relevant and special attention has been paid to advanced processes such as, for instance, the welding of batteries using increasingly sought after materials such as copper and aluminium.
In these cases, several manufacturers have developed composite coaxial fibres to modulate the intensity of inner and outer fibres (cladding) independently. The selection of certain profiles provides pore-free welding, with more adhesion and less spattering.

Beam guiding for industrial processing
Fundamentally, laser beam guiding is provided by fibre optics, although there are cases in which the characteristics of a laser, the CO2 laser for instance, require that guiding be performed through the air and by means of conventional optics. Whether it be fibre or air, laser emission is inserted in a head where, by means of a lense or mirror system, it is possible to focalise the beam and aim it at the sample.
In the case of fixed optics heads, the beam always impinges statically on the optics and it it’s the movement of the head or the sample or both that determines the radiation pathway on the material. Typical process based on this type of head are, among others, laser cutting, microperforation or LMD (Laser Metal Deposition) additive manufacturing.
Fixed optic heads also contain gas injection systems to confine the work area, avoid oxidation or minimise the area affected by heat.
In recent years, sensors have been increasingly installed in heads to perform online process monitoring and service heads on a real-time basis.
There are clear examples such as the use of hyperspectral cameras, thermographic sensors or distance measuring devices based on OCT technology OCT (Optical Coherence Tomography).
Galvanometric scanners offer an alternative to fixed optical heads. In this case, the laser beam is redirected by two mirrors towards focusing optics. The XY movement of the mirrors determines the work area on the sample without having to move the head or part.
Solutions of this kind are suitable whenever the following is required: high processing speed (maximum galvanometric scanner speed is 5m/s), large working distances (>100mm) or complex beam movements over the sample. The use of wobbling strategies (rotating on the axis) offers a clear example in these battery welding operations.
As occurs in the case of fixed optics heads, significant developments have been reported with respect to the onset of new scanning solutions.
Polygonal scanners allow maximum processing speeds of 100 metres/second to be achieved thanks to rotating mirrors. By combining these components with the growing presence of high repetition frequency pulsed lasers (>4MHz) it is nowadays possible to introduce the laser technology in high speed (5min/m2) surface texturing processes to compete against more traditional process such as chemical etching or shotblasting.
Similarly, there are different components such as Diffractive Optical Elements (DOE) or Spatial Light Modulators (SLM) that allow the original beam to be split into several beams that can be modulated independently and enable parallel processing. These technologies are increasingly being used to improve productivity in additive manufacturing processes or for high-speed marking, for example, to generate up to 100 different QR codes per second.
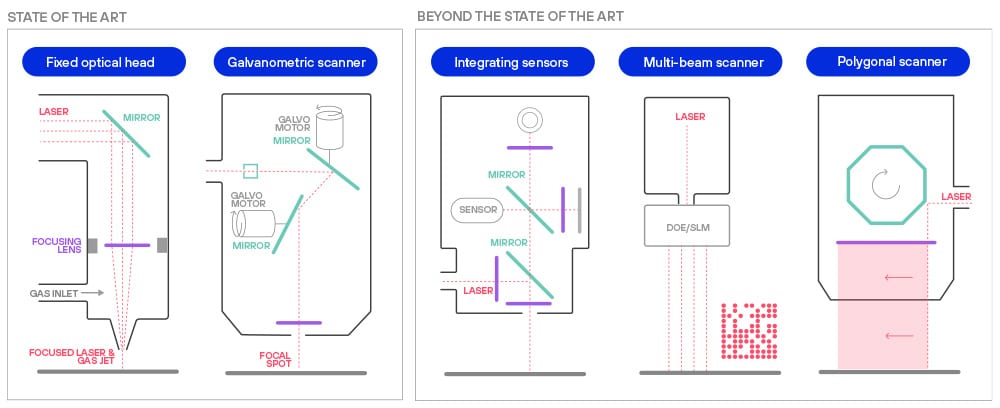
Integrating the industrial laser system in machines/robots
The full integration of all the components in a processing system is the final step to obtain an industrial laser system integrated in a machine and/or robot. In this regard, there are two possibilities: integrating a laser system in a numerical control machine (CNC) or in a robotic arm. Once again, this decision fundamentally depends on the specific requirements of the manufacturing process based on the laser under consideration.
Therefore, a CNC solution is suitable in those situations in which special requirements must be met in terms of processing speed, reliability and accuracy. CNC machines are particularly suitable for micromanufacturing processes such as precision cutting or microperforations.
On the other hand, and by fitting laser systems on robotic arms it becomes possible to increase system resilience, extend working areas and the geometry ranges that lasers can reach in processes that do not require high accuracy positioning. Examples can be found in additive manufacturing using LMD or in hardening and tempering operations, among others.
The Laser Manufacturing Lab in Tekniker
Finally, it is important to point out the capabilities of the Laser Manufacturing Lab in Tekniker.
The technology centre has a laboratory equipped with 16 industrial lasers, different types of heads and machines (both commercial and in-house manufactured) for a large range of industrial processes: from welding, cutting or cladding to high-precision processes such as microperforation or texturing.
Thanks to its high degree of specialisation in this area, the centre can also monitor these processes, address the optical design of components and manufacture complete industrial solutions.
An example of the value attached to the Laser Manufacturing Lab in Tekniker in terms of laser technologies can be seen in what we have called TITAN, a machine used for the additive manufacturing of large components (>1.5m3) in metal, that has been fully developed at the centre that includes a deposition head and has implemented a wire LMD process to achieve high productivity levels (>5kg/hour) when manufacturing parts.
1 Annual Laser Market Review & Forecast 2020. Laser Focus World, January 2020