PROJECTS
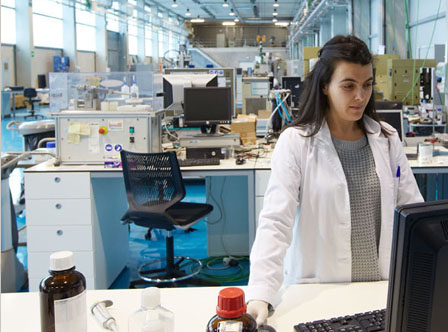
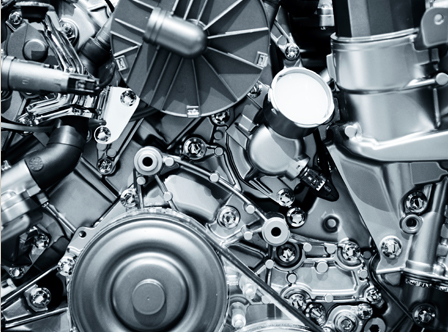
After work spanning three decades for countless industrial clients like EADS, FIAT, CAF and Repsol, IK4-TEKNIKER’s tribology unit is now in a consolidated position as a benchmark player in industry offering consultancy services and supplying solutions in this field.
With its activity recently boosted by its new facilities, IK4-TEKNIKER’s Tribology Unit service has 16 researchers working to come up with solutions for problems relating to friction, wear and lubrication.
Although Tribology continues, on the whole, to be a field that companies attach only relative importance to, tribological phenomena in any mechanical component exert a direct impact on economic questions, like energy saving, owing to the reduction in friction, or savings in maintenance costs due to less wear.
Aware that national industry has been lagging quite a long way behind in recent times in comparison with international industrial sectors, IK4-TEKNIKER's Tribology service has been responsible for gradually introducing the most up-to-date tribological techniques and concepts into Spanish industry.
Its work has helped to achieve the cost-cutting aims of major industrial companies, including ones that are worlds apart like Orona or Gamesa, since friction, wear and lubrication are phenomena present wherever there are moving parts in contact with each other. That is why the range and field of application of this discipline are huge for a whole host of sectors: automotive, aeronautical, energy, health, etc.
Consulting
IK4-TEKNIKER's service in the field of Tribology sets out to use a range of experimental techniques that make it possible to analyse the friction produced in the contact between materials in relative motion with each other, as well as the wear they are subjected to. Through studies of this type it is possible to compare different materials, surface treatments and lubricants working in conditions similar to those while in service. Researchers at the R+D centre conduct not only approval tests but also tests designed in accordance with the specific needs of each customer. There are two types of tests: one type tests actual components like gears and bearings, and for this purpose IK4-TEKNIKER's new facilities have a specific test bank. The other type are simulation tests, which work with samples of materials to test their wear resistance.
In both cases these are relatively short, low-cost tests in comparison with what is involved in tests on an actual component.
But IK4-TEKNIKER's Tribology Unit does not restrict itself to tests of this type. It also conducts diagnostic tests dealing with the cause of breakdowns, application of coatings with tribological functionalities, analysis of used oils, studies into joint compatibilities or the design and characterization of oils, in addition to other capabilities.
In addition to having participated in over 120 European, national and regional projects and being involved in organising the Tribology conferences IBERTRIP and LUBMAT, IK4-TEKNIKER's specialised team represents Spain in various international working groups and associations like the Virtual Tribology Institute, Tribology COST 516, and the Eureka Network ENIWEP for Wear Prevention.